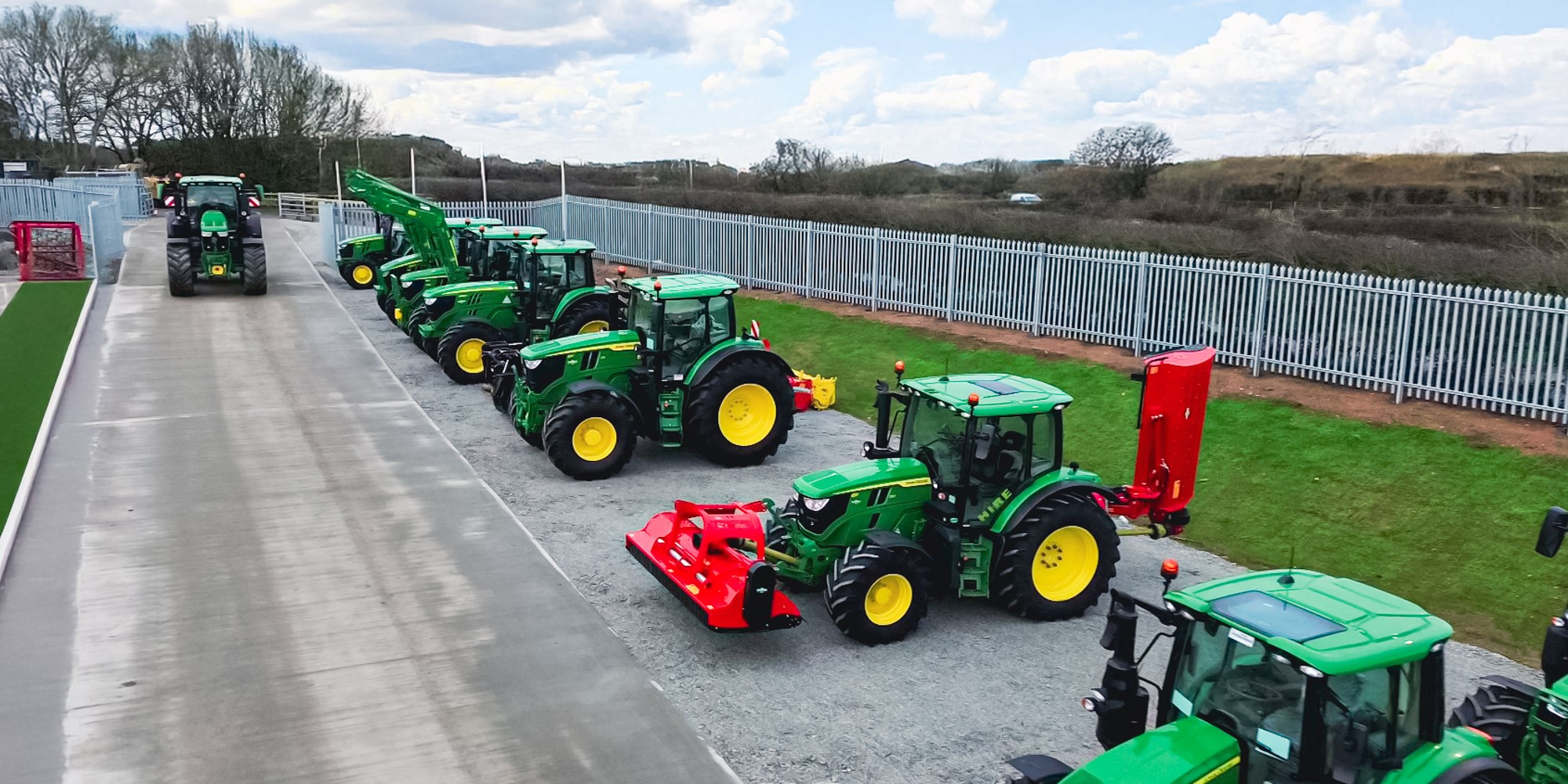
As more tractors, telehandlers, mowers, and spare parts continued to arrive, their existing space wasn’t enough. Keeping things organised was becoming a more significant challenge every day, and customer service efficiency was at risk. Graham Furse, Group Parts Manager, knew something had to change. They were rapidly running out of space, and with demand continuing to grow, it was clear something had to change. A brand-new depot was built in a prime location, close to busy transport links. But more space alone wasn’t enough, they needed a smarter way to store parts, streamline workflow, and ultimately, deliver an even better service to their customers.
Finding the Right Solution
Graham and his team weren’t just looking for shelving. They needed a long-term storage solution that could evolve with their business. Having used Dexion products in the past, they knew they could rely on their durability and quality. When the time came for an upgrade, partnering with Dexion again was an easy decision.
The solution was the Hi280 multi-tier shelving system, a high-capacity, heavy-duty storage solution designed for businesses with high-volume inventory and limited floor space.
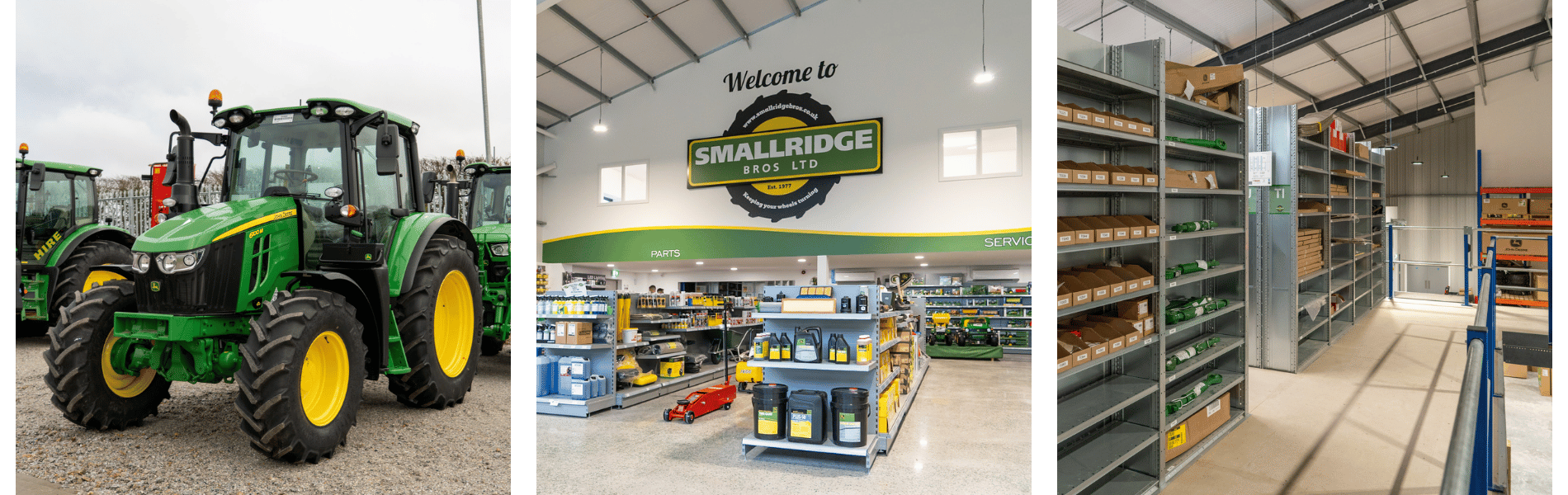
Instead of occupying more ground space, the Hi280 enables businesses to build upwards. This allowed Smallridge Bros to maximise every inch of their depot while enhancing accessibility to their stock.
The warehouse space for trade counter companies like Smallridge Bros is often restricted. Therefore, maximising storage capacity and enhancing operational efficiency are vital. The Hi280 system accomplished this by offering various bay depths, providing flexibility for their diverse product range, showcasing Dexion's capabilities and Smallridge's adaptability.
Why did they choose Hi280?
- More Storage Capacity – A multi-tier system that could store significantly more parts without requiring a larger footprint.
- Improved Organisation – Everything neatly arranged and easy to find, reducing wasted time searching for parts.
- Faster Customer Service – When parts are easy to locate, repairs happen more quickly, keeping customers happy.
The decision was made. Now, it was time for the transformation.
"Previously, our parts department was cluttered, causing difficulty locating items, with constant issues making room for new items. Now, with our storage solution, we are able to spend time speaking to and assisting our valued customers whilst working with a system where there’s a place for everything and room to grow for years to come."
- Graham Furse, Group Parts Manager
The Installation: More Than Just Shelving
In October 2024, installation work began. Callum Hall, Dexion’s Sales/Installation Manager, led the project, ensuring the shelving system was installed efficiently and tailored perfectly to Smallridge’s needs.
The new multi-tier system was designed to:
- Streamline their workflow, making it easier for staff to move efficiently through the depot.
- Improve stock management, reducing misplaced or lost parts.
- Enhance service operations with a dedicated parts counter for quicker customer interactions.
With their newly organised workspace, the team could now service a wider range of machinery, giving customers better support than ever before.
The Impact: A Game-Changer for Smallridge
Once the new storage system was in place, the results were immediate...
Hi280 in a multi-tier application with a mezzanine floor
More Space, More Inventory
The new storage system allowed Smallridge Brothers to stock a wider range of parts, reducing delays and eliminating backorders. No more waiting. No more "we’ll have to order that in." Just fast, reliable service.
Faster, More Efficient Service
For farmers, downtime isn’t just an inconvenience. It’s costly. With the Hi280 system, Smallridge staff could now locate and retrieve parts in quickly, drastically reducing the time customers are without their essential equipment.
A Clean, Organised Workspace
In their old depots, parts were stacked wherever they could fit. The depot felt cluttered and chaotic. Now, everything has a designated place. The warehouse is tidy, structured, and easy to navigate, a massive improvement for both efficiency and team morale.
Happier Employees
A better system doesn’t just benefit customers. It makes employees’ lives easier too.
- No more frustrating searches for missing parts.
- No more wasted time sorting through cluttered shelves.
- Just smooth, streamlined operations that make the job more enjoyable.
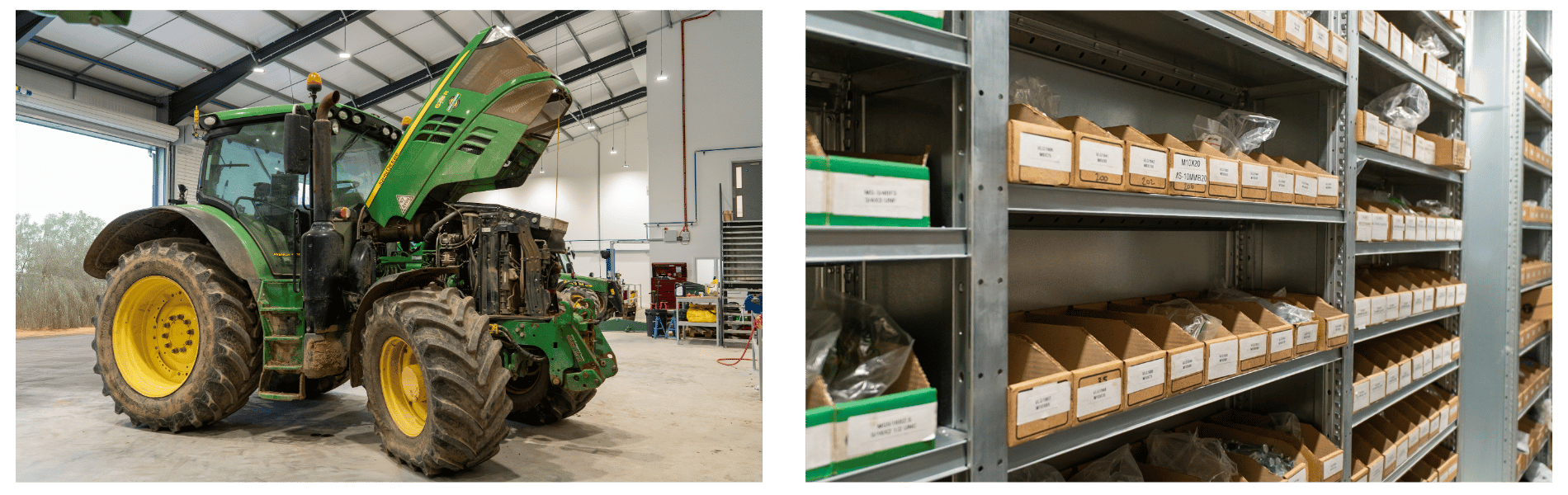
A Better Customer Experience
At the end of the day, everything Smallridge Bros does is about supporting their customers and the local economy. With an optimised storage system, a dedicated parts counter, and an improved servicing area, they can now:
- Offer faster repairs and minimise machinery downtime.
- Keep a larger inventory to meet demand.
- Provide a better overall customer experience that keeps farmers coming back.
Looking Ahead
For the Smallridge Bros, this investment isn’t just about shelving. It’s about supporting their future growth. With a smarter storage system in place, they’re better equipped to serve the farming community for years to come. The right storage solution doesn’t just transform a warehouse. It transforms an entire business. Smallridge Bros is proof of that.